Robot 4 control methods, you know how many?
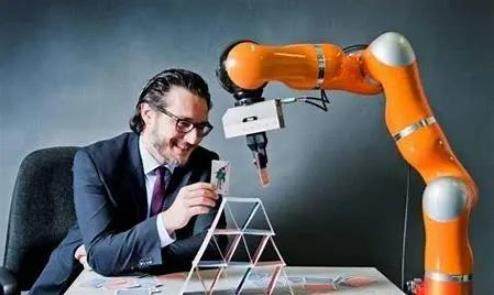
At present, the most used robot in the market environment is industrial robot, which is also the most mature and perfect robot, and industrial robot can be widely used, thanks to its various control methods.
Robot control can be divided into joint space control and Cartesian space control. For serial multi-joint robots, joint space control is for the variables of each joint of the robot, and Cartesian space control is for the variables at the end of the robot.
According to the different control amount, robot control can be divided into: position control, speed control, acceleration control, force control, force mixing control and vibration control.
According to different operations, it can be mainly divided into four control modes: point control mode, continuous trajectory control mode, force (torque) control mode and intelligent control mode! What are the functions of these 4 control methods?
01. Point Control Mode (PTP)
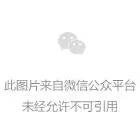
This control method has a wide range of applications in the field of mechatronics and the robot industry! The position of the end effector of an industrial robot on some specified discrete points in the work space is controlled. In the control, only the industrial robot is required to be able to move quickly and accurately between neighboring points, and the movement trajectory to reach the target point is not specified.
Positioning accuracy and the time required for movement are the two main technical indicators of this control mode. This control method has the characteristics of easy implementation and low positioning accuracy, so it is often used in loading and unloading, handling, spot welding and inserting components on the circuit board, which only require the target point to maintain the accurate position of the end actuator. This way is relatively simple, but to achieve 2 ~ 3um positioning accuracy is quite difficult.
02. Continuous Trajectory Control (CP)
CP control is to continuously control the position and posture of the end effector of an industrial robot in the working space. The speed of the middle point is not 0, and the speed of each point is obtained by means of velocity foresight. General continuous trajectory control mainly uses the speed foresight method: forward speed limit, corner speed limit, backward speed limit, maximum speed limit and contour error speed limit.
This control method requires it to move strictly in accordance with the predetermined trajectory and speed within a certain precision range, and the speed is controllable, the trajectory is smooth, and the movement is smooth, in order to complete the task.
Each joint of an industrial robot moves continuously and synchronously, and its end effector can form a continuous trajectory. The main technical index of this control method is the trajectory tracking accuracy and stationiness of the end-effector position of industrial robots, which are usually used in arc welding, painting, burring and inspection robots.
03. Force (moment) control mode
With the continuous expansion of robot application boundaries, visual enabling alone can not meet the complex practical applications, at this time, it is necessary to introduce force/moment control output, or force/moment as a closed-loop feedback quantity into the control.
When assembling, grasping and placing objects, in addition to requiring accurate positioning, the force or moment used must be appropriate, and the (moment) servo mode must be used. The principle of this control method is basically the same as the position servo control principle, but the input and feedback are not position signals, but force (moment) signals, so the system must be a force (moment) sensor. Sometimes the sensor functions such as proximity and sliding are also used for adaptive control.
04. Intelligent control mode
The intelligent control of the robot obtains the knowledge of the surrounding environment through the sensor, and makes the corresponding decision according to its own internal knowledge base. Using intelligent control technology, the robot has strong adaptability to the environment and self-learning ability.
The development of intelligent control technology depends on the rapid development of artificial intelligence such as artificial neural network, genetic algorithm, genetic algorithm and expert system in recent years. This control mode makes industrial robots really have the taste of "artificial intelligence", but it is also the most difficult to control well, in addition to the algorithm, but also relies heavily on the accuracy of the components.
In recent years, the intelligent control technology has made obvious progress, fuzzy control theory and artificial neural network theory and the fusion of the two have greatly improved the speed and accuracy of robots. The main applications are multi-joint robot tracking control, lunar robot control, weeding robot control, cooking robot control, etc.
With the blessing of intelligent control technology, industrial robots are truly intelligent, but it is also the most difficult to achieve, and it relies heavily on algorithms and components.